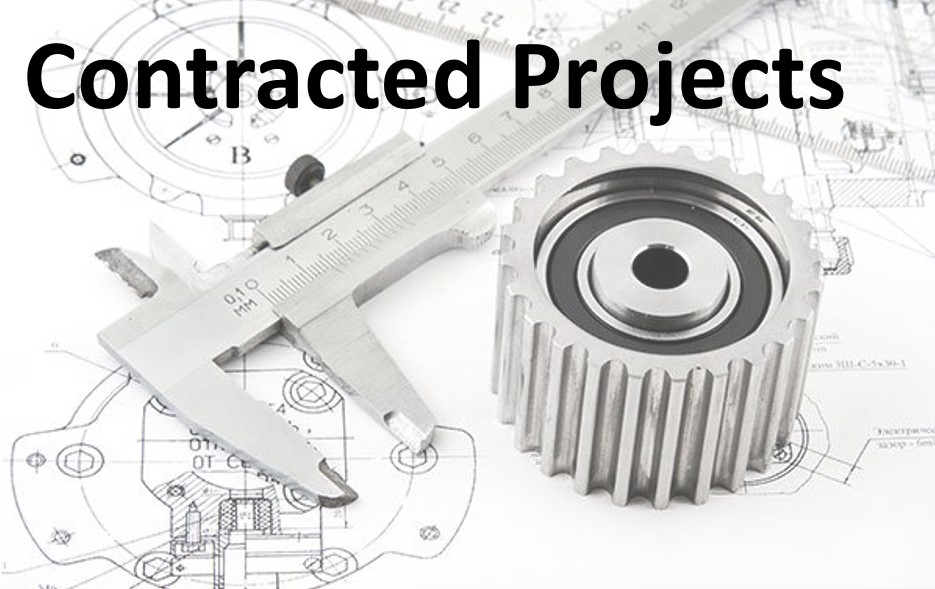
Since 2010, we have been doing contract work with companies. Many of these projects include engineering services to design and prototype a new product for a local customer. Industrial partners vary and include biomedical companies, the department of defense, aerospace, and the construction industry. Projects often involve students where I help to train the next generation of engineers in practical product design and development methods, engineering analysis techniques, and professionalism, while simultaneously meeting our customer’s needs for high quality engineering services.
MÄGERLE MFP30 Dressing Roll Hoist
GE Aerospace is a world-leading provider of jet engines, components, and integrated systems for commercial and military aircraft. The capstone team build a custom hoist to lift a tool dressing roll out of a manufacturing machine for servicing. The design used thin lower legs to slide under the machine and a pneumatic cylinder to raise and lower the heavy steel dressing roll during removal and installation. A challenging design requirement to safely hold the load even when air pressure was lost was overcome using pilot controlled check valves. We developed a custom design using 3D CAD modeling, optimized the design using finite element analysis, and built it for our customer. As an added touch, the team laser cut and installed the GE logo. Image shows the team and our customer (red and blue shirts).
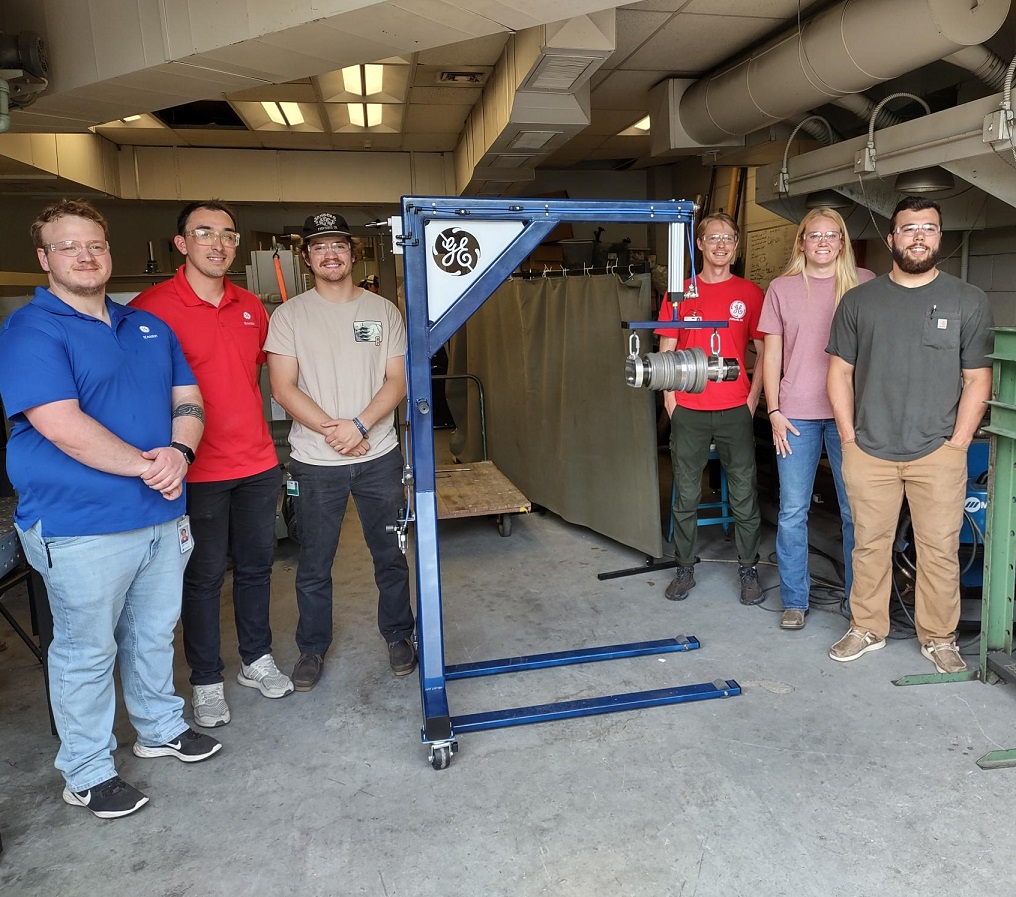
V22 Osprey - Dummy Input Quill
Naval Air Systems Command (NAVAIR) provides support for the United States Navy’s aircraft and airborne weapon systems. We designed and built a device used for servicing the V-22 Osprey vertical takeoff and landing aircraft. The device attaches to the proprotor gearbox and hold the aircraft engine during servicing. We developed the design based on customer drawings of the actual input quill. Our device had the capability of being used for servicing on either side of the aircraft by rotating 5 degrees around the central axis, eliminating the need for two separate devices. Once designed, we used finite element analysis to properly size the components to support the weight of the engine at every angle from zero to 90 degrees.
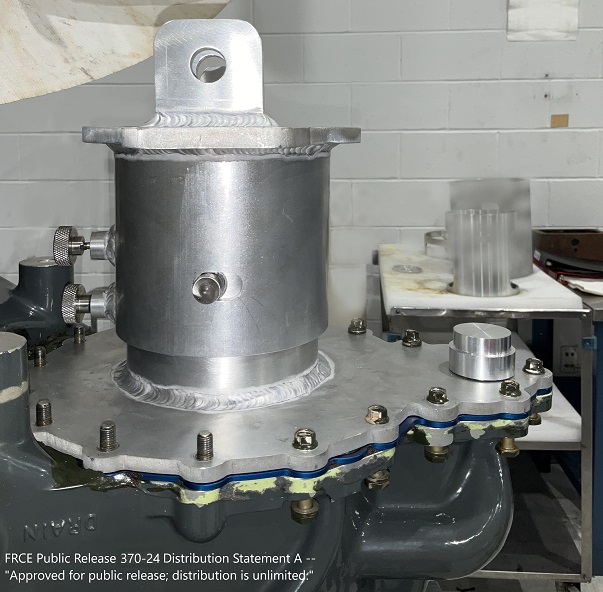
Under Road Boring Machine
TK utilities is a construction company in Asheville. We designed a structure to support a boring machine that is able to drill holes under roads and concrete for passing wires and pipes. Our product enabled the boring machine to be placed into a hole and adjusted in place eliminating the need to place it in and pull it out multiple times to get the boring machine properly aligned for drilling. We developed a custom design using 3D CAD modeling, optimized the design using finite element analysis, and built it for our customer.
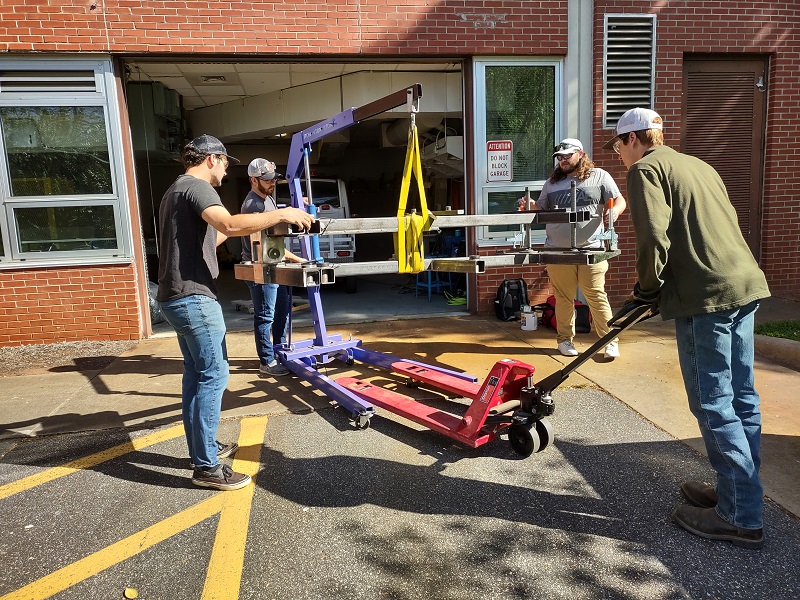
F35 Jet Fighter Engine Removal Trailer
Naval Air Systems Command (NAVAIR) provides support for the United States Navy’s aircraft and airborne weapon systems. We designed a device to remove the almost 5,000 pound fully loaded engine from the aircraft for maintenance and repair. We worked with NAVAIR engineers to understand the customer needs and developed a design using 3D CAD modeling. We then used finite element analysis to determine stress levels in the design and strengthened it where needed and changed the design to reduce cost for areas where the initial concept was over designed.
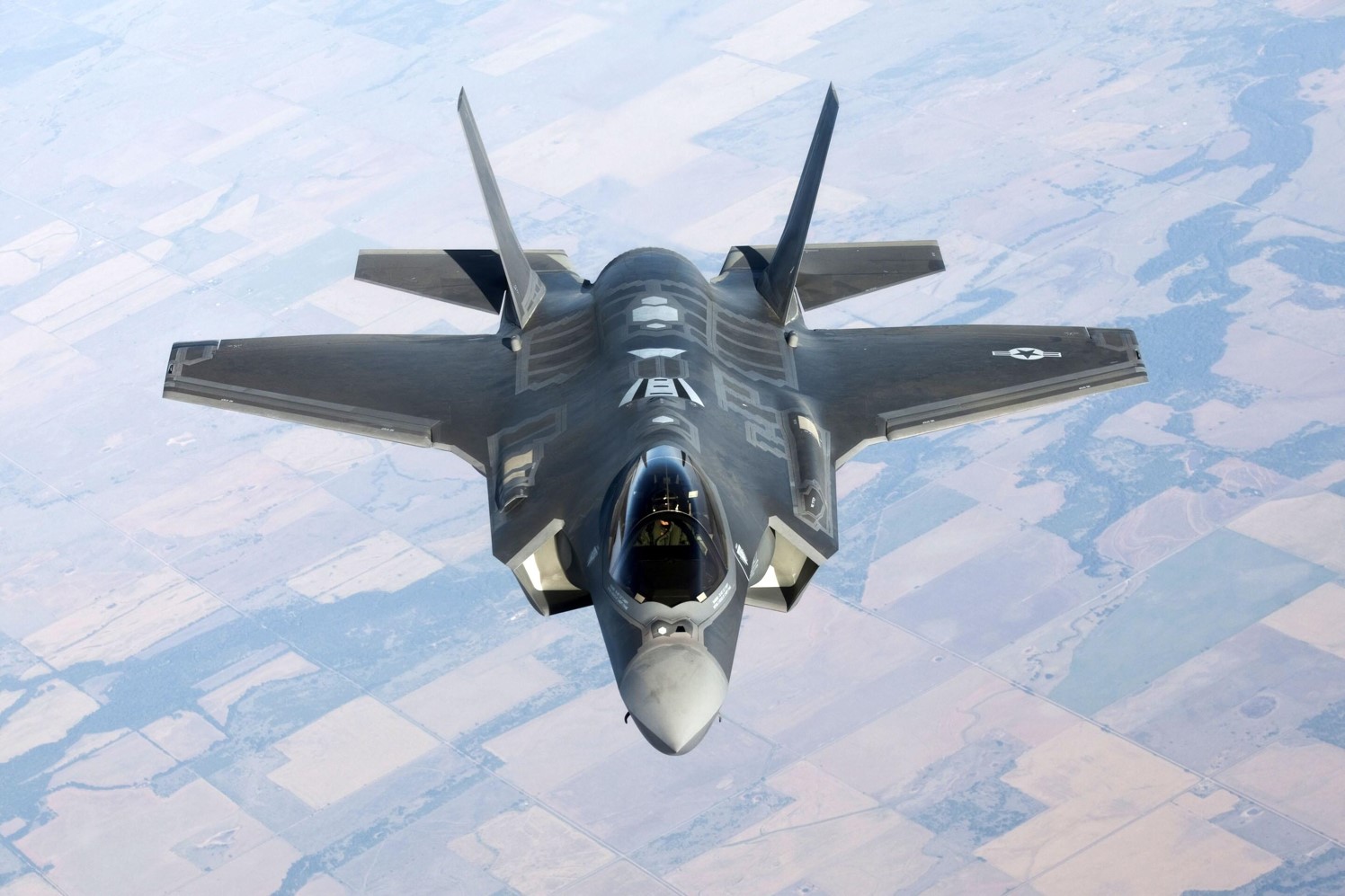
H53 Helicopter Oil Cooler Enhancement
Naval Air Systems Command (NAVAIR) provides support for the United States Navy’s aircraft and airborne weapon systems. The Sikorsky H-53 Helicopter has been used by the U.S. Marine Corp to move people and equipment since 1966. To meet modern requirements, we designed a new oil cooler to enhance the heat transfer. We created the new design using 3D CAD modeling and analyzed the performance using Computational Fluid Dynamics (CFD). Performance was optimized based on CFD and the design was provided to the customer.
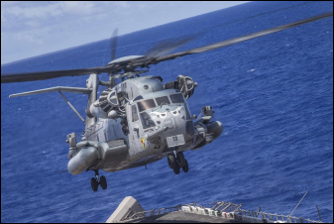
C130 Aircraft Propellor Lifting Device
Naval Air Systems Command (NAVAIR) provides support for the United States Navy’s aircraft and airborne weapon systems. The Lockheed C-130 Hercules is an American four-engine turboprop military transport aircraft used by the U.S. Marine Corp. We designed a portable lifting device to enable Marines to replace propellor blades in the field to recover downed aircraft. Working with our customer, we created a design using 3D CAD modeling and analyzed the performance using finite element analysis (FEA). Our initial concept was overdesigned in several areas, and results from the FEA enabled us to reduce cost and weight prior to building the first prototype.
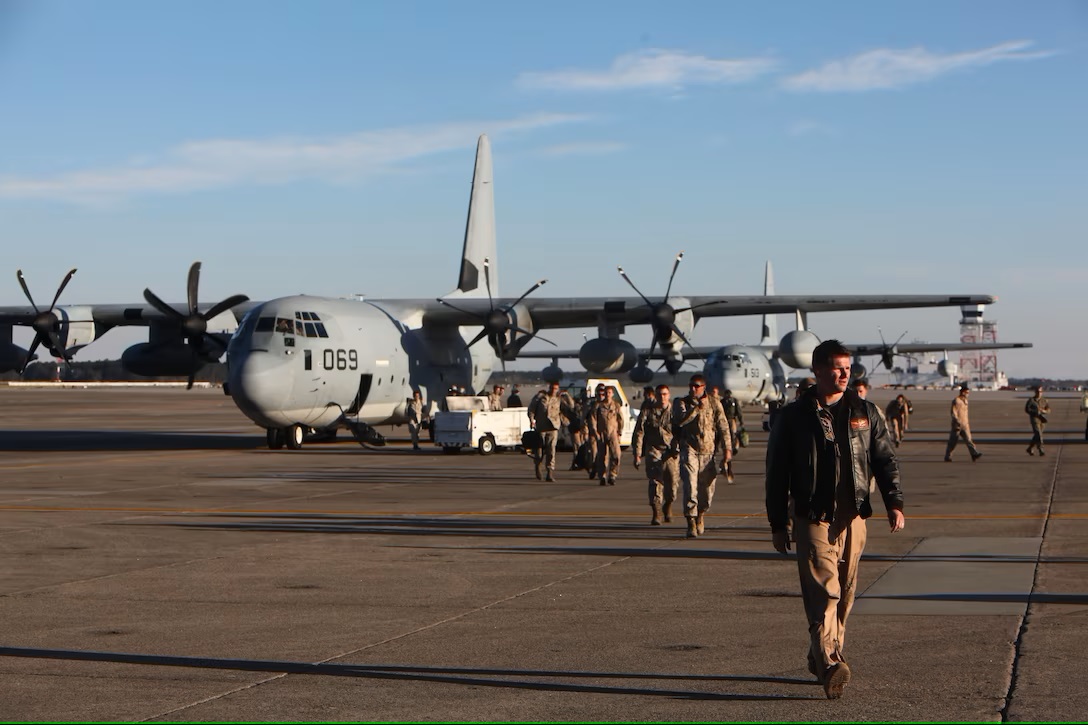
Probabilistic Risk Assessment for a Small Modular Reactor
The U.S. Nuclear Regulatory Commission (NRC) was created to ensure the safe use of radioactive materials for beneficial civilian purposes while protecting people and the environment. In the nuclear industry, probabilistic risk assessment (PRA) is crucial in providing insights into the strengths and weaknesses of a plant’s design and operation. In this work we created a PRA model for a loss of coolant event in a light water small modular reactor (SMR) and used it to suggest safety improvements.
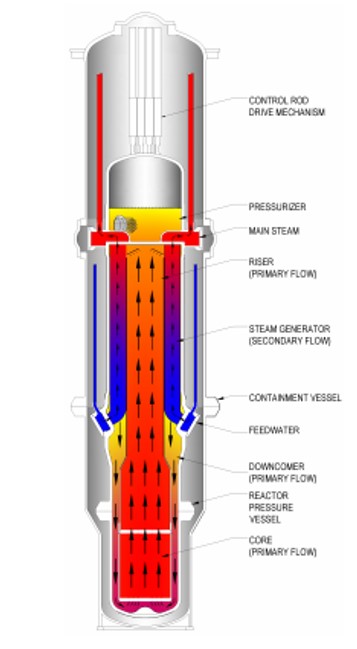
Endoscope Tube Tracking Device
A gastroenterologist in Sylva North Carolina. He hired us to develop a new endoscope tube tracking device. The goal was to track the movement of an endoscope to examine a location in the esophagus and return to the same location months later to see how the area had changed. A team of senior design students developed an electronic device using time of flight (similar to GPS) to determine the location within the body. An engineering analysis showed that time of flight could not be used because processing speed would need to be higher that current electronics are capable of achieving. The team eventually developed a second approach that tracked the distance the tube traveled and the amount it rotated based on the technology used in an optical mouse.
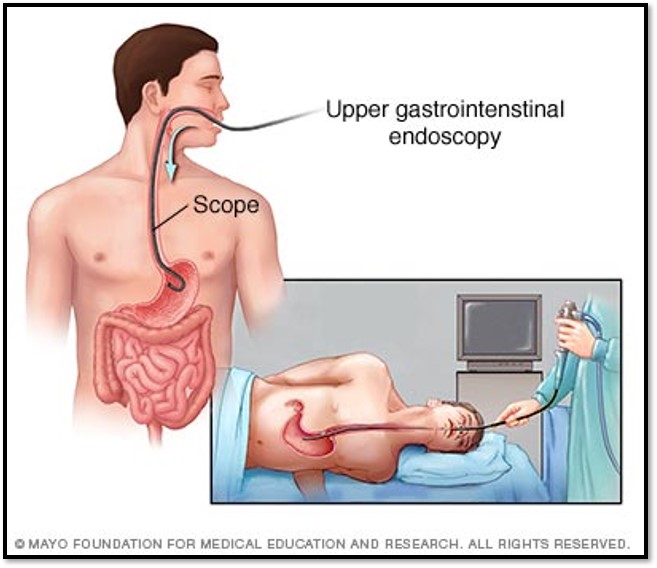
Personnel Locating Device for Aircraft
Naval Air Systems Command (NAVAIR) provides support for the United States Navy’s aircraft and airborne weapon systems. Many Naval and Marine Corp missions are in extremely harsh environments which makes it difficult for pilots to maintain situational awareness inside the aircraft. We designed a passive device to locate Marines and Sailors within the aircraft using a multiple camera system. A novel component of the design was that each person could be located using a single camera and accuracy could be improved using multiple cameras.
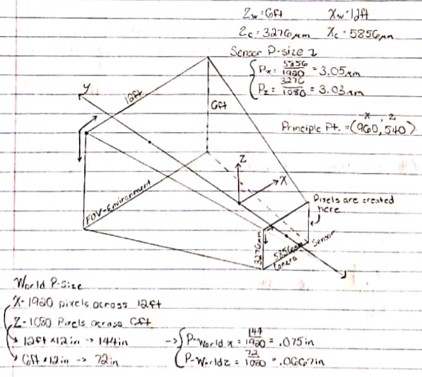
Aifcraft Engine Analysis Equipment Design
Naval Air Systems Command (NAVAIR) provides support for the United States Navy’s aircraft and airborne weapon systems. Jet engines are tested to ensure that they meet performance specifications. We designed and built and Aerothermal Analysis Device that connected to a multitude of thermocouples to measure the temperature of the air exiting the engine in different locations. Our device also had several transducers to measure pressures. Finally, we wrote a LabVIEW program to interface with the DAQ and display the aircraft engine temperatures and pressures in a graphical format.
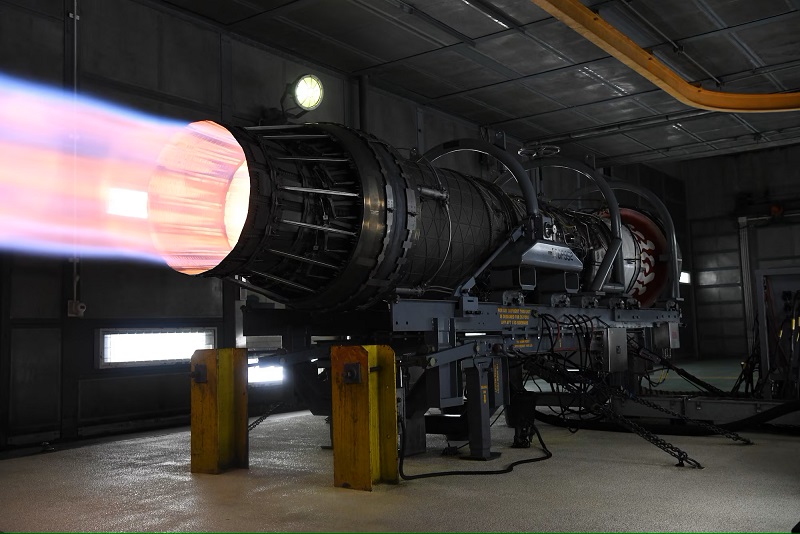
Extending Aircraft Propellor Life in the V22
Naval Air Systems Command (NAVAIR) provides support for the United States Navy’s aircraft and airborne weapon systems. The V22 Osprey is a vertical takeoff and landing aircraft designed to combine the functionality of a conventional helicopter with the long-range, high-speed cruise performance of a turboprop aircraft. The propellors have heating blankets to reduce icing which require regular maintenance. Our project was to investigate why electrical conductors were breaking and to develop a potential solution to extend propellor blade life. We developed 4 new designs and built a cycle tester to evaluate them. The existing design failed within 1,000,000 cycles and our best new design was still working well at 2.2 million cycles when we ended the test.
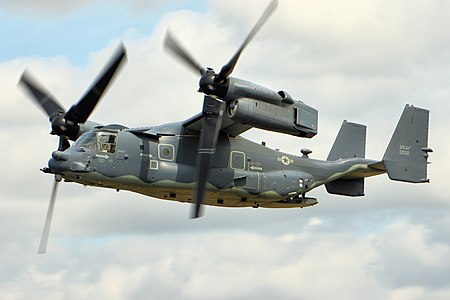
Medical Device for Sinus Surgery
An ear nose and throat surgeon in Raleigh, NC. He hired us to develop a new device for sinus surgery. Current devices on the market use separate devices to open sinus passages and to irrigate the sinuses to remove material and apply medication. The device our student team designed did both operations simultaneously with a single device. Because Tanaka had prior patents, he was aware of the process and worked with the students and inventor to apply for a patent which was awarded in 2022 – United States Patent Number 11,229,447. Recently the surgeon’s company obtained approval from the US Food and Drug Administration (FDA) to manufacture and market the device.
Collapsible Large Diameter Endoscope Tube
A gastroenterologist in Sylva North Carolina. He hired us to develop a new endoscope tube that is collapsible and also able to expand to a larger diameter. A team of senior design students met with our customer to understand his vision for the product and develop an understanding of the customer needs. The team generated several conceptual designs, selected one of these to develop, developed the detailed design, built a prototype and tested it.
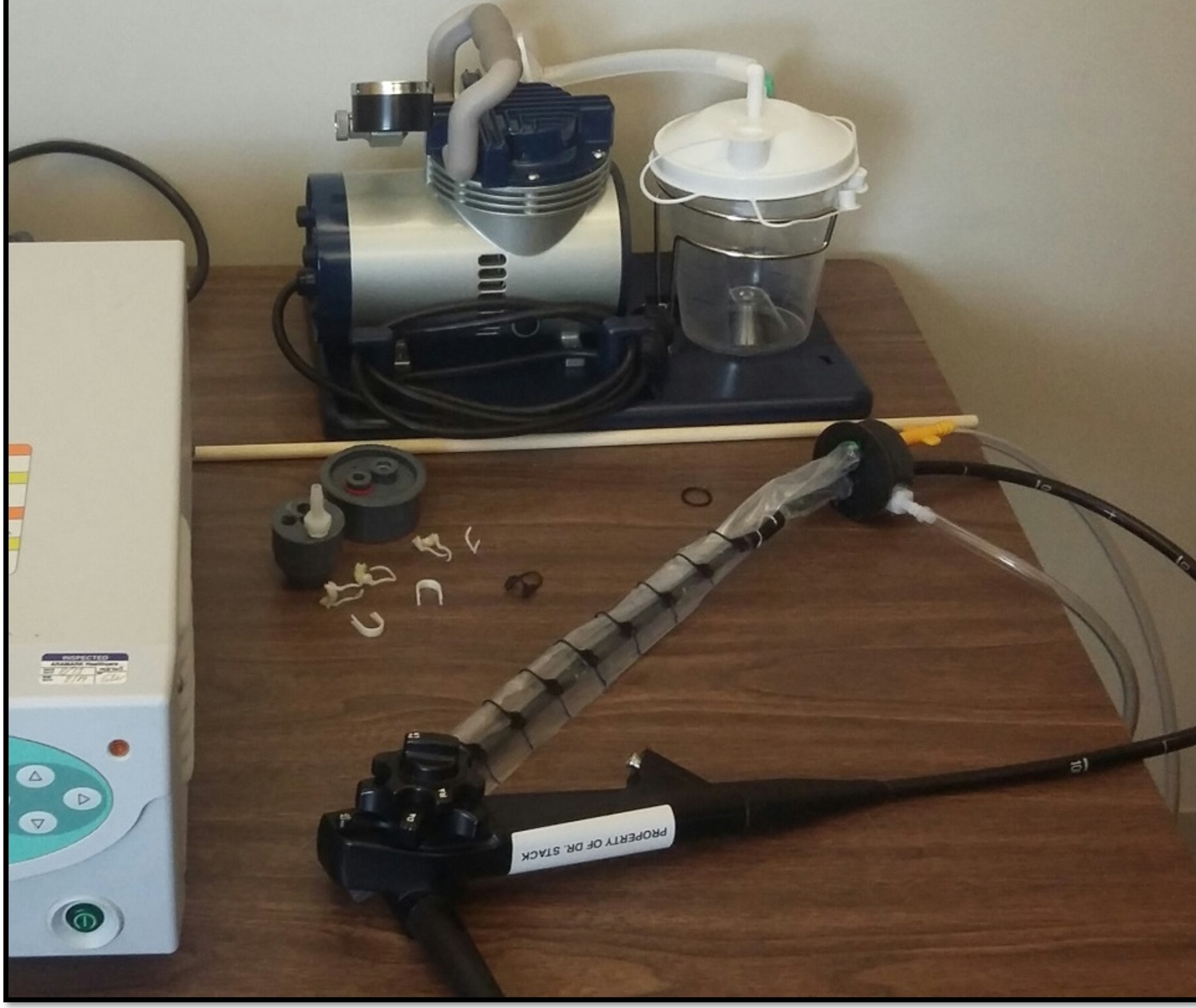
Luxury Wheelchair
An entrepreneur in Niagara Falls. One of his businesses is a hotel within walking distance of the falls. He hired us to develop a luxury wheelchair to assist people who may not be able to walk to the falls on their own. This assistive medical device could be used for people with limited mobility that do not have access to a powered wheelchair while traveling. Such a device could enable a person with a broken leg to join their family and avoid remaining at the hotel. Our student team developed a device based on tank turning, built the device and tested its performance.
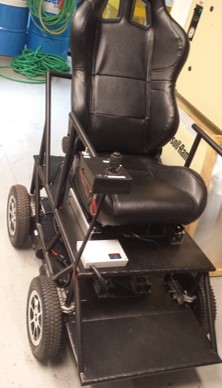
Powered Hoist
An entrepreneur near Chapel Hill North Carolina hired us to design and develop a powered hoist to list people from bed using an overhead track. He was a return customer who wanted to upgrade the manual hoist developed previously (see below) to enhance its capabilities. The new assistive medical device was developed by a new group of students who were not aware of the previous manual hoist project. They developed several conceptual designs and eventually selected a design the utilized a worm gear and worm (like the previous team). They used an electric motor to drive the worm, powering the hoist.
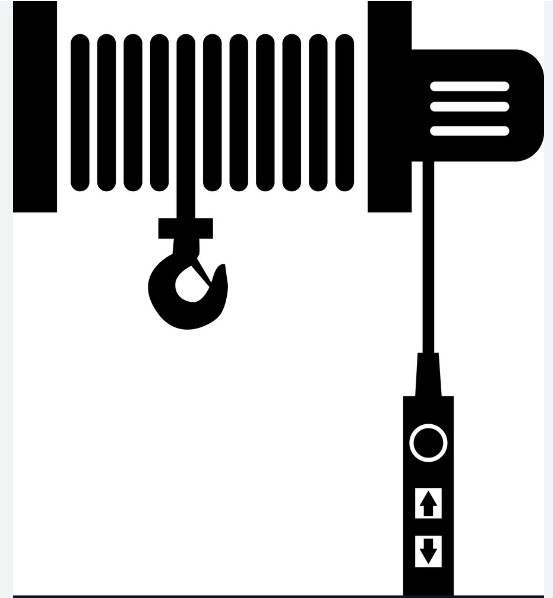
Manual Hoist
An entrepreneur near Chapel Hill North Carolina hired us to design and develop a manual hoist to list people from bed using an overhead track. This assistive medical device could help a smaller or older person lift a spouse that was incapable of moving themselves. The customer specified that the hoist must be capable of lifting 400 pounds and not backspin which could put a person being lifted at risk of falling. The students designed a system including a metal worm, worm gear, crank arm, and housing. The housing was printed from ABS using an industrial quality 3D printer. When assembled and tested, the device safely lifted 400 pounds of sandbags.
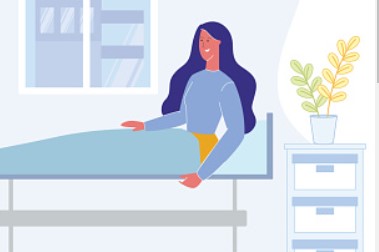
Design and Development of a Ceramic Heater
A company in Arden North Carolina hired us to design and develop a ceramic air heater capable of heating air to very high temperatures using ceramic foam. Ceramic foam is a robust material that is highly heat resistant. One of its uses is to filter debris from molten steel. A student team designed and built a prototype. When they tested the device, air temperatures exceeded the thermal meter’s maximum value. As the test continued (we tested to failure), the stainless steel housing began to glow dull orange and bright orange before the device failed. Overall, we determined that this technology was a viable approach, and we provided this information and our test results to the customer. Our customer was very pleased with the project and funded multiple additional projects in future years.
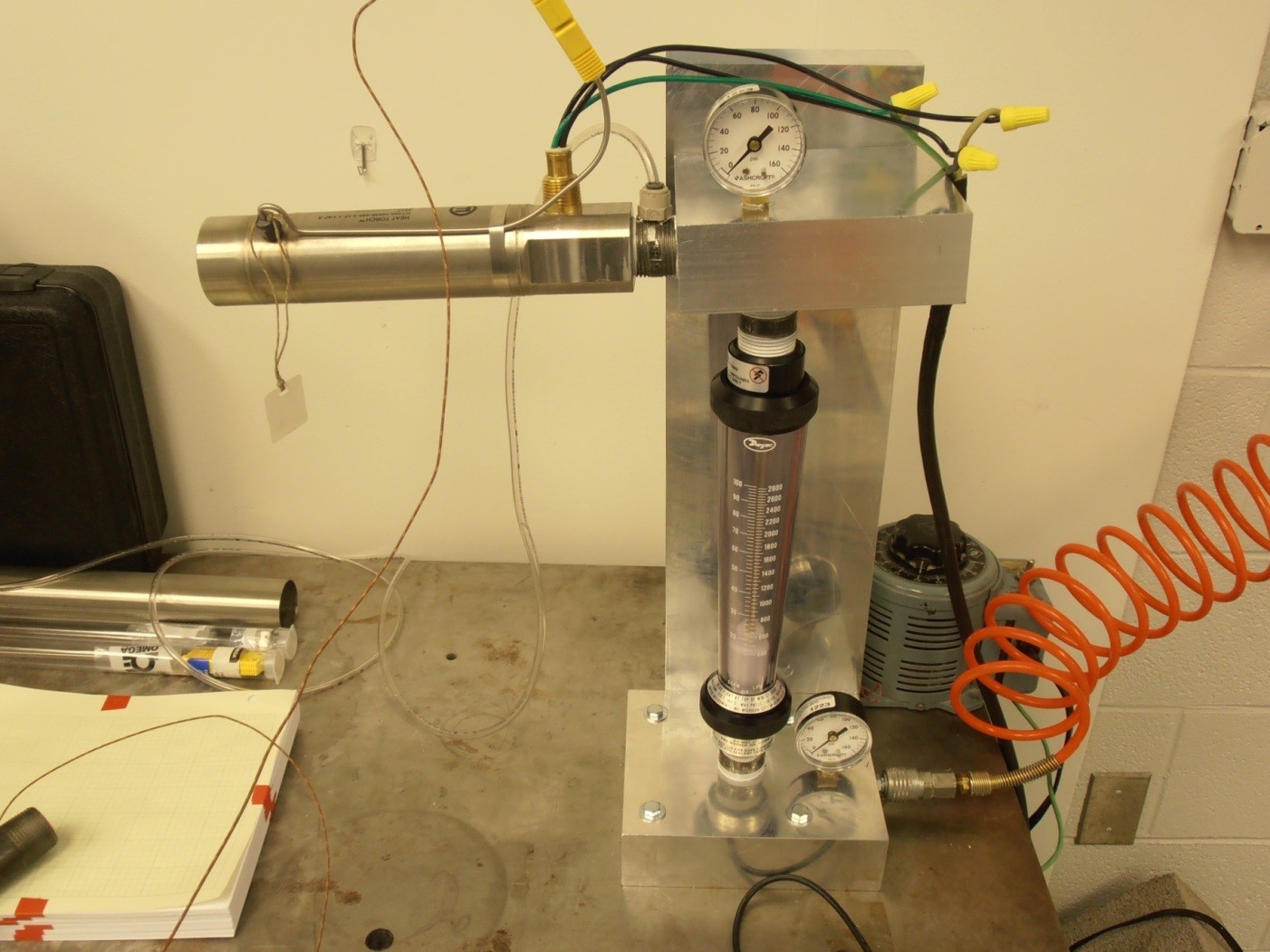
Compression Garment Donning Device
An individual in Chattanooga Tennessee hired us to design and build an assistive medical device to help a person with lymphedema (the elephant man) to put on a compression garment. Compression garments provide external pressure to a limb that helps to minimize fluid retention. Like a wetsuit, these garments can be difficult to put on. To address this, we developed a device that uses body weight to spread the garment open and allow the person to step into the garment. We submitted our design to the undergraduate design competition in assistive medical devices and it was selected as a finalist. The national science foundation (NSF) paid for the student team to travel to Pennsylvania and present their design at the competition. Although we did not win, the students had an opportunity to present their work at a professional conference and see presentations of other students and faculty.
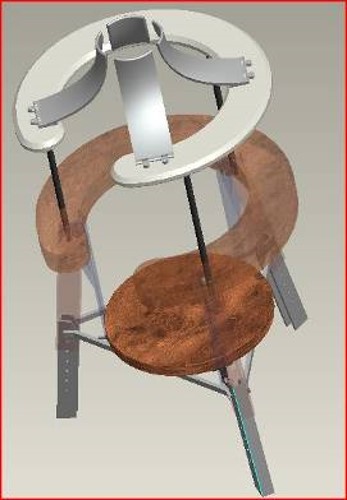